日本林內瀨戶工廠自動化生產制造:處實效功,謀定而后動
? ? ? ? ? ? ? ? ? ?本文由 電器雜志 發表,轉載請注明來源!
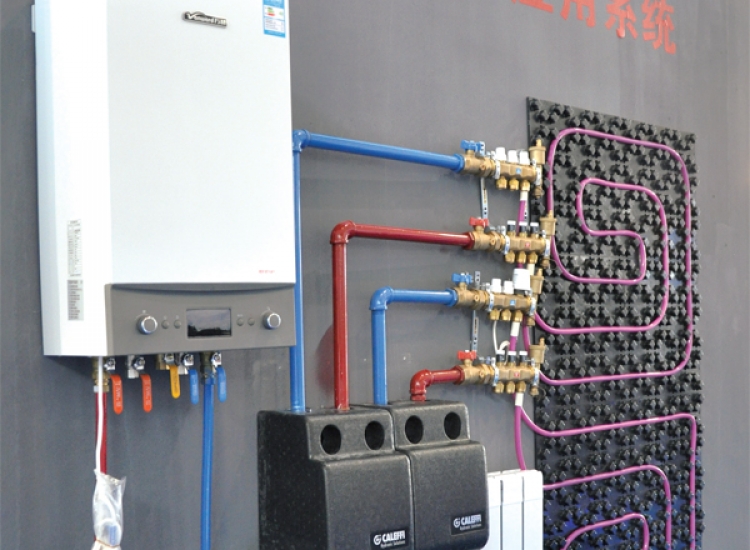
2017年12月19日,離開位于名古屋愛知縣的大口工廠,《電器》記者驅車大約25公里來到林內旗下的另一個重要工廠??瀨戶工廠。這是記者一年中的第二次到訪,而此次的采訪重點也從上一次的“工匠精神”變成了“自動化生產與制造提升”。當記者向再一次見面的瀨戶工廠工廠長松本和彥詢問,瀨戶工廠自動化生產制造改善最突出的成果和特點有哪些時,他的回答十分質樸:“我們進行的自動化生產改善解釋起來很簡單,就是盡最大努力去簡化不必要的生產中間環節,提升生產效率,節約生產費用,并且實現更高的品質。這是我們工廠進行任何生產改善的初衷,同時也是林內集團所有工廠生產制造自動化改善的整體思路。”
通過細致的參觀與走訪,《電器》明顯感到,瀨戶工廠自動化生產制造的出發點就是如此清晰明了,而“處實效功,謀定而后動”已基本能夠概括其自動化生產改善的特點。
目標清晰的制造升級
瀨戶工廠是林內集團最大的熱水器生產工廠,始建于1979年,占地42649平方米,其中生產用地面積約13683平方米,主要生產即熱式燃氣熱水器和綜合熱能熱水器等產品,年產量達到92萬臺,出口量在22萬臺左右。
瀨戶工廠由四大部分組成,包括生產熱水器中主要部件無氧銅制熱交換器、不銹鋼潛熱式熱交換器及部分水路連接件的第一工廠,作為鈑金部門的第二工廠,組裝生產線的第三工廠等。以“工匠精神”和“精益制造”理念立身的瀨戶工廠,每天都在進行著細微的生產改善活動,其中也包含著生產自動化改善的部分。
瀨戶工廠副工廠長豬瀨洋志就對記者介紹,在瀨戶工廠,上至工廠長下至每位員工,參加改善活動可以說是他們工作的重要內容之一。“在員工隊伍中,七個人為一個改善小組,每個星期都會組織一次活動,每個月進行一次比賽,一年舉行做一次大型報告。”豬瀨洋志告訴《電器》記者這是日本林內工廠最常規的作法,其中也包含自動化改善的活動。
對于這座每天都進行著各種生產改善的工廠,身處其中的人或許早習以為常,而距上次到訪相隔已近一年的《電器》記者卻發現了諸多細節的變化。
在參觀瀨戶工廠燃燒器的制作工序時,《電器》記者發現,原本的做法是將原材料用沖壓機床沖壓好之后,需要由工人把它放到一個盒子里送到下一個步驟的加工機床部門。現在這個步驟經過改善,從原材料鋼板進入沖壓機床到最后制作成型已經完全實現自動化,每分鐘可以生產35個燃燒器。“這個工序的改善不僅減少了人工,還大大提高了效率,并且產品品質也得到了保證。”陪同《電器》記者參觀的松本和彥對于這一自動化改善的成果十分滿意。
記者注意到,這種用機械手替換連接環節的人工,將更多的設備合理串聯起來,是瀨戶工廠自動化生產改善常用的手法。在參觀過程中,“這里減少了1個人,那里原本的機器只是單獨的一臺,現在連接成了整整一段工序”這樣的講解經常出現在耳邊。
對于瀨戶工廠2017年生產自動化改善的目標,松本和彥透露:“通過合理的設備投入和生產方式改造,我們的目標是整個工廠減員16名,到12月,實際的結果是減員12名。”
瀨戶工廠原本的自動化程度并不低,16名操作人員的減員目標并不是輕而易舉就能實現的,需要通過大量的改善行動來實現。
在參觀熱交換器的生產線時,記者發現一個上次參觀工廠時沒有注意到的設備,借助一個機械手、兩片銅板可以自動壓制成一個盒子形狀的殼體,而加工成型的熱交換器盒里的連接管(出水管、進水管)也全部實現了自動焊接。“以前是人手工焊接,現在至少節省了一個人工。”松本和彥說。
此外,在熱水器本體外殼的加工程序中,《電器》記者也看到,這里也新增了一臺自動加工殼體的機械手,一整塊鋼板在它的操作下被迅速折成長方形殼體的三個平面,后面的機械手則負責給加工好的外殼上鉚釘。松本和彥告訴記者:“現在一個工人就能完成四道工序,大大提升了效率,這樣的機器人在林內中國工廠也有應用。”
客觀理性的自動化改善
“品質和成本是我們行為準則的兩個基本要素,我們希望用自動化來改善品質和降低成本,但是一定會客觀計算和衡量好利弊得失,如果自動化能降低成本,卻影響品質,那我們就不會實現那個工序的自動化。”當記者問到評判和衡量工序需要自動化的標準,松本和彥的回答十分客觀理性。
確實,“視品質為生命”的林內會將此作為任何行為的第一考量要素。記者在參觀熱交換器的生產線時注意到,瀨戶工廠的一項特殊工藝。當熱交換器中注入焊接液,放入有精準溫度控制的焊接爐中進行加工。它的獨特之處在于進行了無氧燃燒處理,銅材質的熱交換器外表不會變黑,焊接煅燒過程要經過整整十個小時。面對記者對此零部件并非外觀件卻還要注重美觀性的疑問,松本和彥的解釋是,不僅是外表,林內產品對內部件的美觀性也十分講究,并且在有氧和無氧兩種狀態下制作出來部件的耐腐性也有所不同。
此外,在不銹鋼冷凝式熱交換器生產線上,一個正在給熱交換器涂著焊接液的機械手吸引了記者的注意力。林內工作人員告訴記者,這個機器中間有一個照相設備,可以通過照相來確定熱交換器的型號尺寸和位置,并決定采用怎樣的程序來控制涂焊接液的數量、均勻度和時間。機械手按指示位置涂焊接液,比原來人手去涂均勻得多。
“零部件、核心技術和生產裝備的原廠自制”是林內保證產品品質的重要“法寶”。在進行自動化生產和制造提升的道路上,林內也同樣遵循這樣的法則,瀨戶工廠幾乎都是結合自己的生產實際需求,同時利用外購的機械手進行整個機器自動化改造。許多機器上都標有亮眼的“Rinnai”的標識。
在偌大的工廠中,松本和彥給記者指出了許多這樣的生產設備。據他介紹,林內的熱交換器吸熱片是由自己制作,一個熱水器中共有63張,第一張到最后一張形狀都不相同,而眼前的機器已經能夠實現從左邊將原材料放入,全部采用機械手自動打印,打印好的銅片就自動放入一個箱子里,實現一體化生產。這臺林內自制的設備一分鐘至少可以制作300張熱交換器吸熱片,最多時可制作330張。
瀨戶工廠對于自動化設備的投入絕不是盲目的,會充分考量投入產出比。松本和彥指出:“我們會合理計算自動化設備投入產出及節約的用工費用之間的成本對比,脫離實際地進行設備投入,這在瀨戶工廠甚至整個林內集團都是不被允許的。”
對自動化設備投入的時間節奏控制,瀨戶工廠也有自己的準則。“我們通常是在新產品開發時,才會考慮投入新設備。現在要生產更多高性能產品,自然就會投入更復雜的設備” 豬瀨洋志為記者講解,“我們申請做設備投入也需要一定的流程,首先要寫申請書得到上級批準,然后從購買零部件,再到研究組裝完成,至少需要6個月的時間。”
豬瀨洋志進一步舉例,瀨戶工廠中一個制作風機中風輪的自動化設備整整用了兩年的時間才研發成功并投入生產。之所以會用如此長的時間,就是因為風輪轉速不好就會產生噪聲,并影響整體燃燒效果。“我們一定把設備性能做到最好才正式使用。”豬瀨洋志說。
整體來看,瀨戶工廠的生產自動化改善是按照自己既定的路線在有條不紊地向前推進。同時,它自動化生產的理性色彩還體現在對舊設備的珍視與改造上。《電器》記者在瀨戶工廠中見到一臺至今已經運轉27年的進水件生產設備,瀨戶工廠沒有直接將這臺設備淘汰,而是在設備中間增加三臺機械手鏈接,取代了操作這臺設備的3個工作人員。松本和彥表示,這臺設備最終要改善成用一臺機械手就能完成操作,以提升效率。
注重人的價值的自動化
日本“工匠文化”的一個重要體現就在于,在任何生產制造的過程中,“人的價值”都是不能被磨滅與輕視的。對于日本企業而言,員工是最重要的價值,對人的信任遠勝于對設備、數據和系統的信任,所有的自動化或是信息化的最終目的都是怎樣更好地為人的工作提供幫助。在林內瀨戶工廠進行生產自動化現狀走訪之時,《電器》記者也清晰地體會到這一點。
當自動化使生產設備的精準度變得更高,并且自動化檢測設備的投入越來越多,是否就意味著人工檢測環節的省略與減少。對此,松本和彥表示,增加自動化設備一定程度上確實可以提高檢測精度,但是日本法律有明確規定,燃氣產品涉及使用安全性,除了設備檢查,用人眼和人的嗅覺進行明火檢測是必不可少的。“現在瀨戶工廠,生產線上檢測人員的數量已是最底限的規定,即使增加設備,有些人工檢測的步驟也是不能省略的。”松本和彥稱。
在瀨戶工廠,《電器》記者看到的實際情況印證了松本和彥的話,在許多關鍵工序除了采用自動檢測設備,都會有具備專業資質的員工進行人眼檢測,比如在熱交換器焊接完成后,都會有工人拿著一個一個用眼去檢查。
此外,在瀨戶工廠用機械手代替人工的過程中并沒有摒棄“工匠的價值”,在機械手的開發過程中,在運動程序里加入模仿熟練老工人的手法,使匠人的寶貴經驗同自動化改善更好地融合在一起。在冷凝式熱交換器的生產線上,一臺機械手就正在模擬工人將一個部件對著兩個孔口伸插進去,在從另一端抽拽一下,一系列連貫的手法仿佛一個熟練的工人一般。
記者了解到,在瀨戶工廠從事各項工作的員工有806名。許多制造生產中的創意與應該就來自員工的智慧。在瀨戶工廠的組織車間有一條特殊的生產線。據林內工作人員介紹,這是一條完全不用能源的組織流水線,整條組裝線巧妙地利用機械重力原理、滑輪原理及精準的傾斜度等,它的出現就是員工平時進行改善時產生靈感并將之付諸實踐的結果。
在《電器》記者采訪的最后,松本和彥告訴記者,瀨戶工廠目前正在進行制造的轉型升級,將簡單的低附加值產品的生產移至其他關聯工廠,轉而生產更多的高附加價值產品,生產這類產品對生產效率將提出更高要求,因此,瀨戶工廠近兩年將在生產設備自動化方面有更多投入,以此來提高整體的生產效率。
本文由 電器雜志 發表,轉載請注明來源!