黃石東貝:助推“四省”,智造升級加速定制化進程
? ? ? ? ? ? ? ? ? ?本文由 電器雜志 發表,轉載請注明來源!
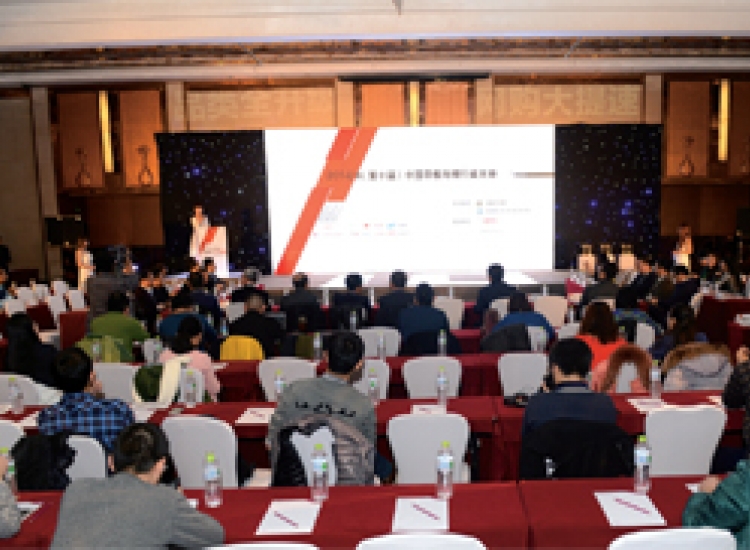
智能制造已成為制造業發展的必然趨勢。智能制造升級既符合中國制造業從“制造大國”向“制造強國”的轉型要求,也能提質增效,節約社會資源并降低成本,同時還能滿足日益提升的定制化市場需求。11月17日,在“尋找中國家電業智能制造先鋒大型主題活動”期間,《電器》記者來到黃石東貝電器股份有限公司(以下簡稱黃石東貝),通過采訪以及對“最前線”的實地參觀后發現,黃石東貝正在描繪一幅高效靈活的生產模式、產業鏈有效協作與整合、新型生產服務型制造、協同開發和云制造的智能制造藍圖。
“四省”
關于智能制造升級對制造環節的提升,黃石東貝電器股份有限公司工程部部長尤瓊兵用了“四省”來總結。所謂“四省”,分別為省人、省力、省耗以及省心。他進一步解釋說:“省人,是指精益智能化可以相對減少用工;省力,是指針對勞動強度比較大的崗位,通過智能化改造,減少人的勞動強度;省耗,是指智能制造升級可以減少能源消耗,降低制造成本;省心,是指以前很多需要人工收集的質量和檢測數據在智能化升級后可以由系統自行采集和反饋,并全流程跟蹤質量情況。”
《電器》記者在參觀黃石東貝標桿生產線時,對這“四省”有了深刻地感受。在省人方面,記者粗略地數了一下,整條生產線的員工不足40人。據黃石東貝電器股份有限公司副總經理朱宇杉介紹,改造前該生產線需要80位員工。令《電器》記者印象深刻的是,對產品質量影響較大的焊接工序,黃石東貝已經實現自動化升級,通過機器人來節省人力,5臺焊接設備僅需要1位工人操作管理即可。尤瓊兵提供的黃石東貝三大基地2014~2017年人數曲線圖呈明顯下降趨勢,也可以印證智能制造升級對人員減少的影響。該數據顯示,截至2017年10月,黃石東貝三大基地人數較2015年減少1268人。
朱宇杉進一步介紹道:“以前僅跑合線這一道工序就需要十幾人,智能化升級后,現在5個工人就足夠了。這對效益和效率都有提升。但也產生了一個問題:對設備維修人員的技術水平要求提高了。人才儲備變得更為重要。”
在參觀過程中,整條生產線并未見到需要人工搬運等勞動強度大的工序。黃石東貝機電集團有限責任公司總裁朱金明指出,越來越多的“90后”“95后”開始進入工廠,他們對工作環境要求更高。“而且,黃石東貝所在的地理位置并不利于招工。因此,對于勞動強度較大的崗位,我們會優先考慮設備自動化升級。”
產品質量和生產效率提高
黃石東貝智能制造升級后,另外一大特點就是質量管控得到提升,產品質量的穩定性提高。參觀變頻壓縮機標桿生產線時,朱宇杉告訴《電器》記者,這條生產線經過對設計、供應、質量和過程控制四方面的提升,生產出的產品可以做到10年質保。“在智能制造升級后,我們產品設計的可靠性得到提高;在供應鏈方面,可以通過系統對比各項數據選擇優質的供應商,保證零件的可靠性;在質量和過程控制方面,不僅通過質量管理控制,還通過對員工定員定崗來控制。”
信息化時代,數據變得非常重要。朱金明表示:“過去,生產時的質量數據都靠人工收集,不僅復雜,而且容易造成誤差,致使數據分析出的結果不夠準確。信息化后,生產時的重要數據都可以由系統自動采集,數據實時且準確,分析出的結果對產品設計及質量穩定性也更有幫助。”
朱宇杉指出,經過智能制造升級后,產品質量和可靠性都得到很大提升,標桿生產線不合格產品下線率也因此下降為50ppm~100ppm。據尤瓊兵介紹,宿遷基地新建中的數字工廠也將復制該模式。隨著產品質量的提升,用戶下線率也呈明顯下降趨勢。根據尤瓊兵提供的數據,截至2017年10月,黃石東貝用戶下線率較2014年下降63.64%。
除此之外,智能制造升級也提高了生產效率。據朱宇杉介紹,黃石東貝11條生產線最初產能為2700萬臺/年。在技術改造和智能化改造后,目前已達到3300萬臺/年。其中,變頻壓縮機標桿生產線可達到330萬臺/年。“2018年處,我們宿遷基地新生產線正式投產后,公司總產能將達到3600萬臺/年。除此之外,明年我們還將繼續提高原有生產線的生產效率,最終產量有望達到3900萬臺/年。”
根據黃石東貝十三五規劃,到2020年,在僅增加一條生產線的情況下,經過智能制造升級,黃石東貝產能將由2016年的3300萬臺/年增加到3900萬臺/年,其中變頻產品產量將由300萬臺/年提高至1500萬臺/年,人均效率將由2016年3.2臺/小時到2017年的5.2臺/小時。
加速定制化生產模式
單品種、大批量是傳統制造的特點。先生產再銷售的模式,在一定程度上存在資源浪費。隨著供給側改革,更合理的生產模式是根據客戶需求進行定制化生產。因此,多品種,小批量正成為發展趨勢。“以前是我們做什么,賣給客戶什么;現在是客戶需要什么,我們做什么。這樣更利于中國制造業成本降低,也更符合市場需求。資源利用率提高的同時,也會縮減庫存。”而想要實現這種定制化生產,智能制造升級非常重要。
“傳統的生產線增加一個品種,便需要開一個模具。生產線智能化升級后,只需要在設備數據庫中修改相應的參數即可。”走到變頻壓縮機生產線的一道工序時,尤瓊兵指著一臺設備說,“比如這臺彎管設備,操作人員只要輸入相應的參數,就能實現產品角度變化。”據他介紹,這道工序生產的三根管子,是壓縮機和冰箱連接的部分,分別為吸氣管、排氣管和制冷劑充注管。以前的生產線中,這3根管子的角度等都是標準化的。現在,冰箱企業也開始考慮產品結構、容量、壓縮機位置等,對每根管子的角度都有了不同的角度需求。
“過去,我們只能依靠開模具來實現,但隨著多品種、小批量趨勢愈發突出,開模具成本越來越高。”尤瓊兵進一步說道,“然后我們就在業內率先對這道工序進行了智能化升級,提高生產線柔性。以前我們需要超過100套模具,現在只需要一套設備即可完成。這道工序的自動化升級現在已經在全行業推廣。”
值得一提的是,在尤瓊兵看來,智能制造不是獨立的,而是由上下游相互聯通。就黃石東貝而言,智能制造是由整機企業向我們延伸。“比如客戶會有一些個性化的需求,會通過網絡向我們下單。我們在接到信息后,會將其發給研發部門,然后利用信息平臺對制造系統進行指導。與此同時,我們也會向自己的上游進行輻射,把我們的需求告知供應商。最終實現真正的定制化。”
本文由 電器雜志 發表,轉載請注明來源!